Robotic Design Process
Resources
- Resources
- Knowledge Space
- Robotic Design Process
Robotic Design Process
Have you ever considered the importance of robotics?
In this article, Controls Director - 'Chris Webber' discusses the importance of robotics in automation, how to select the perfect robot for the job and how we commission the robots at 3P.
Why use robots?
We'll first look at the advantages of using robots over human operators. Critically, they offer greater process consistency at a reduced operating cost. Without fatigue, robots can operate overnight, during weekends and with little supervision; performing the same task in the exact same way for as long as need be. In addition to this, a robotic system offers enhanced flexibility over an automated one - once programmed, the robot will switch between different processes with ease, often with minimal or no change parts.
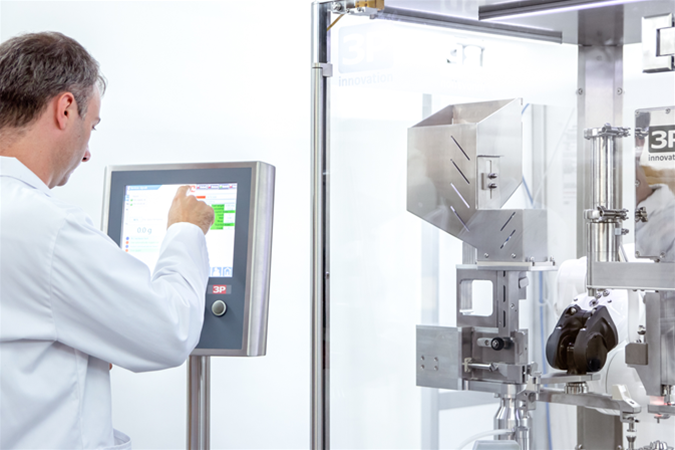
For 3P, an important advantage of robots is improved cleanliness. We operate primarily in the pharmaceutical industry in which the product must be kept sterile. As humans are the largest cause of contamination in cleanrooms it is especially advantageous to use robots where possible.
Identifying your application requirements
Any application requirements regarding the process should be outlined prior to selecting the robot. This includes an breakdown of the process steps that will be performed by the robot, information on the payload (size, weight, special requirements, etc.) You’ll also determine the reach required of the robot and identify the target cycle time of the process at this stage.
There are some less obvious requirements, for example, you’ll need to know which operator intervention is required for the robot cell in both production and maintenance. You'll need to consider whether there are any environmental requirements (e.g. ISO Class 4 compliant robot) and lastly, whether there are any 3rd party interfaces that the robot will need to integrate with. All of these requirements have an effect on the design and layout of the process; once they have been understood it’s time to select your robot and End Effector.
Selecting your robot
Robot and End Effector selection follows an iterative process whereby different robots are tested through simulations until a workable solution is found. An End Effector is the tool mounted on the end of a robot arm to facilitate interaction with the payload. There are many types of End Effector E.g. vacuum, finger-base grippers, vision system, paint gun, welding head. When deciding which to use, its important to consider what behaviour is required under unexpected conditions. End effectors are typically tested early on in the process to ensure they won't pose risk to the robot (or damage the payload).
Safety design and hazard prevention
The use of robots may pose potential threats and there are safety systems in place to mitigate risk. Essentially, the entire robot lifecycle should be considered when looking at the safety of the system. For example, knowing how the robot will be safely lifted in and out of the cell, knowing whether it will operate safely in production and how to maintain it over time (brake replacement). The system may also require additional safety functions such as restricting the robots range of movement to avoid damaging the cell.
When it comes to robot safety there are many potentially applicable standards to consider. ISO 10218 will always be relevant but additionally the designer should consider safety standards relating to Safety of Machinery, safety distances, positioning of safe guards and many others. For any collaborative systems ISO 15066 should be consulted.
Simulation
At 3P innovation, we develop bespoke machinery to perform first-of-a-kind processes. As it is difficult to make changes once the robot cell has been built, we find it advantageous to simulate the robot application as much as possible to de-risk our projects. A CAD model of the robot cell can be used to check for collision, observe reach, cycle time and aid the overall safety of the system.
Commissioning
Once the design has been tested through the simulation and the robot arm has been built, it’s time to commission to robot. At this stage, coordinate frames are set up and the tool centre point offset needs to be taught.
A coordinate frame allows the robot to be moved along axis that make sense for the process. 3P usually set up a coordinate frame to align the robot axis with the machine frame. Additional coordinate frames may be required to simplify the commissioning of the system by aligning the robot cartesian axis with the process e.g. when performing nesting or denesting operations it makes sense to have the robot x axis move along the nest. To teach the machine frame, 3P usually use three dowels in a fixed position, forming a right angle. By teaching all other positions within this coordinate frame, if we ever have to reteach the robot positions we can do so by just redefining the machine coordinate frame using the same three dowels.
When it comes to teaching the tool offset, it is important to have a precise tool centre point. When moving the robot it is likely you will need to rotate around the centre of the tool and any small error in your tool centre point will lead to an eccentric rotation. Some 3rd party tools will come with the tool centre point offset supplied, but for custom made tooling the designer will need to come up with a method of accurately determining the offset. CAD measurements can be used or the tool can be accurately measured but the offset needs to be very precise and we have found that these methods are not accurate enough. When teaching the tool for our R1000 robot cell we use touch probes, two laser sensors and a small program that slowly moves the robot until the touch probe is triggered and until the two laser sensors are broken. The program records the robot coordinate when these events happened and from that figures out the size of the tool.
Validation
The next step of the design process is to test that the robot meets all the requirements identified at the start. These tests are likely to be process dependent but could include tests on cycle time, OEE (Overall Equipment Effectiveness) and material suitability. Additionally, the safety concept for the robotics system need to be validated - ISO 13849-2 specifies the information required for this validation.
Follow this link to watch the webinar: https://youtu.be/8tdhpf3C7Jg