We employed an iterative design approach, rigorously testing multiple powder dosing technologies to identify the most effective solution for the client's needs. Through this, we optimised the system's footprint by redesigning the containers into a square shape.
Automated powder dosing system for R&D
Custom Automation - Case Study
Automated powder dosing system for R&D
Our custom automation expertise enables customers to advance product and process innovation across diverse industries. In this project, we partnered with a client in the R&D sector to develop an Automated Powder Dosing System, addressing inefficiencies in sample preparation.
The Challenge
The client needed to fill a wide range of powders into a dense array for analysis; during which they faced significant operational challenges:
- Time-intensive sample preparation: The existing manual process was slow, limiting the number of samples analysed daily.
- Labour-intensive: Skilled workers were tied up in lengthy preparation tasks instead of focusing on higher-value activities.
- Risk of cross-contamination: Manual handling of multiple powders increased risk of contamination, affecting the reliability of results.
Why 3P innovation?
The client selected 3P innovation based on our deep expertise in powder dosing and our longstanding relationship built on trust and successful past collaborations. Our ability to engineer a customised, automated solution set us apart from alternative suppliers:
“Testimonial from client to be included here.”
Smart Engineering. Innovation Beyond Automation.
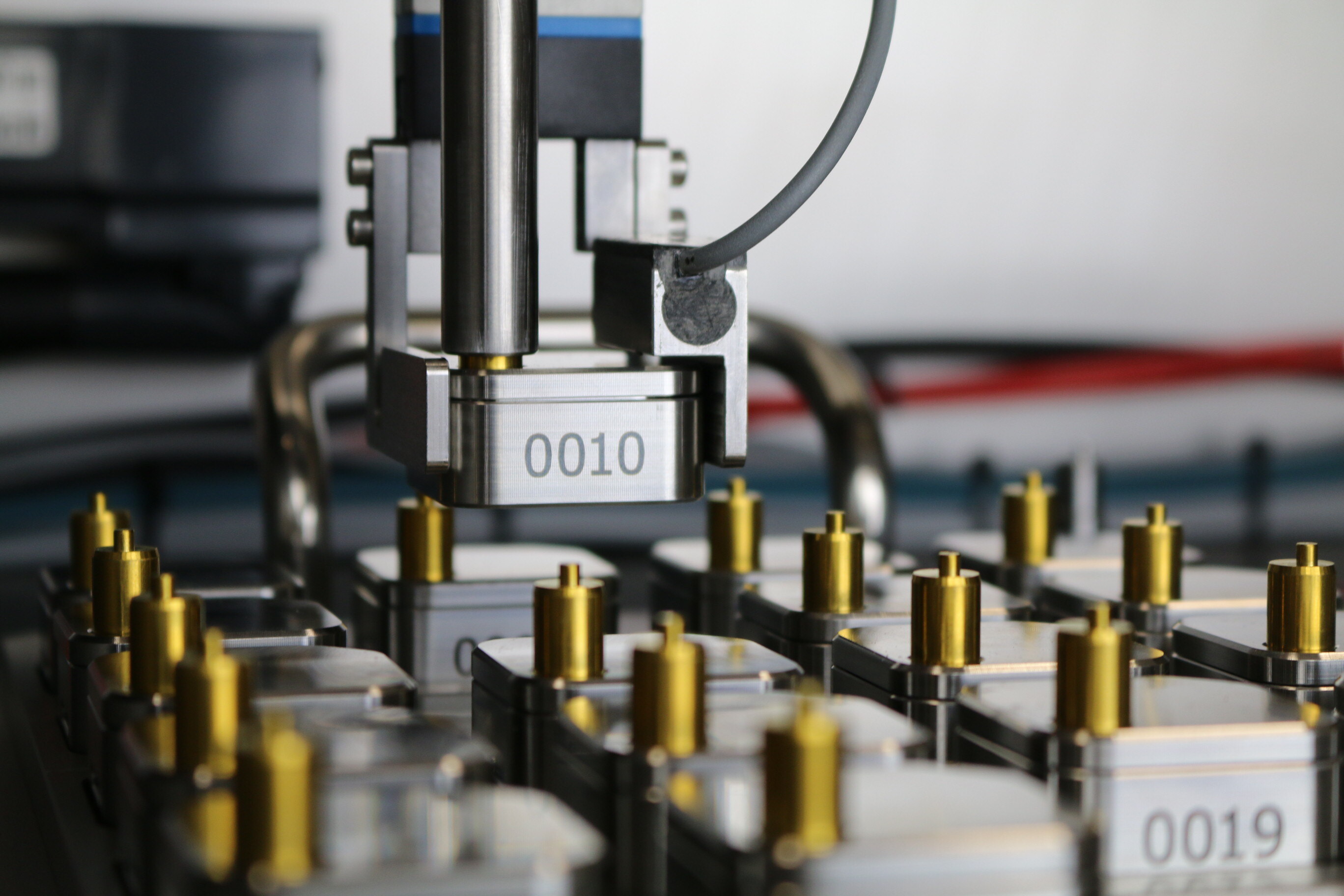
Complex powder handling
The system is compatible with powders of varying chemical and mechanical properties, ensuring reliable, automated dosing.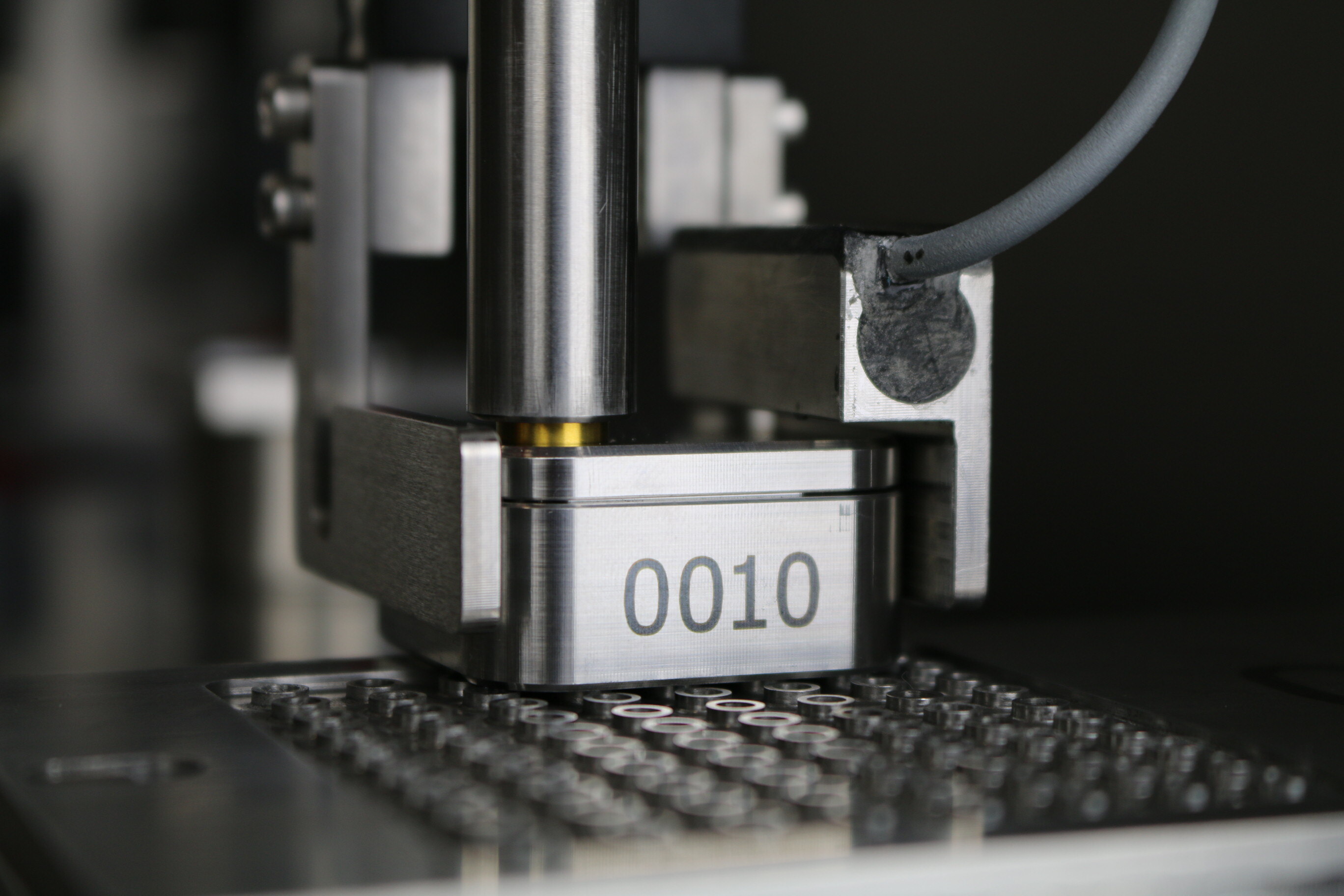
Vibratory dosing technology
The machine incorporates existing technology from our vibratory feeder and doses 80 different powders in one cycle.Our Process
Results and future collaborations
Our machine has delivered transformational improvements for the client, streamlining operations and enhancing overall efficiency. Sample preparation, which previously took 1–2 days, can now be completed within just a few hours. Additionally, the automated design has reduced the risk of sample cross-contamination and allowed skilled personnel to focus on higher-value tasks rather than manual sample preparation.
Building on this success, we look forward to exploring further automation opportunities with this client.
"A quote from the client reflecting their satisfaction with the solution and its impact"